Glaze Theory notes
What is unity formula?
The pdfs available for printouts of the above glazes are from a glaze data base program called Glazemaster. They contain a recipe, but also the unity formula for each glaze.
Unity formula was developed in the late 1800s by Herman Augustus Seger.
It is a way of thinking about the composition of a fired glaze that is independent of the materials used to mix the raw glaze. It is a standard way to calculate and present the relative number of molecules of the various oxides in a fired glaze eg silica, alumina, potassium, calcium etc etc
Unity formula is a representation of the relative number of molecules of each oxide in the fired glaze. Seger chose to calculate these numbers so that the total of all the fluxes always equals 1, with the amount of silica and alumina varying for each glaze.
Nigel Wood in his books prefers to express these numbers as weight percentages (wt%), which is how many grams of each oxide is in 100grams of fired glaze. This is also on the pdf printout.
Mole Percentages simply adjust weight percentages by multiplying them by the molecular weight of each oxide so that the numbers represent the relative number of molecules of each.
Recipe to unity formula is done automatically when you add a batch recipe to Glazemaster. This allows you compare the unity formula to limits, which enable you to predict whether the glaze is likely to suit your purpose. Glazemaster can present each format at if required.
Limits for stable functional ware glazes i.e. durable and hard, resistant to abrasion, acid or alkali attack, without metals leaching from fired surface)
Silica above 2.5 (3-4 is ideal for durability)
Alumina 0.25-0.45
Silica to Alumina ratio 8:1 and above is a glossy glaze
5:1 is matt
Between 8:1 and 5:1 can be either, depending on the fluxes
Fluxes Potassium (K2O) and Sodium (Na2O) 0.1-0.3
Magnesium (MgO) 0.0-0.4
Calcium (CaO) 0.2-0.8
Strontium (Sro) 0.0-0.3
Barium (Bao) 0.0-0.3
Zinc (ZnO) 0.0-0.3
Crazing and Shelling
Crazing results when the glaze shrinks more than the clay body in cooling from the kiln. Because glaze has a relatively poor tensile strength, it will craze to relative tension. It may take some time for the tension to be resolved. A porous clay body absorbing moisture and expending, causing the glaze to craze may also cause crazing. Making the clay body vitreous, or covering all the body with glaze can prevent this.
Alter the glaze recipe to prevent crazing on a vitreous body:
- Replace high expansion materials with lower ones
Fluxes in order of contraction (Rhodes)
Silica (SiO2) 0.05
Alumina 0.17
Zinc 0.07 (used mainly in oxidation firings)
Magnesium 0.45
Boron 0.66
Calcium 1.63
Barium 1.73
Potassium 3.9
Sodium 4.32
- Use the glaze more thinly.
- Fire longer above 1200oC to convert free silica in the clay body to cristobolite, which has a higher contraction. If the clay is contracting more it may match the high contraction of the glaze.
- Change the clay body for one with greater contraction i.e. higher silica like Walker 10 for Keanes 7.
Shivering is the reverse, and you'd take the opposite strategy to correct it. eg use higher expansion fluxes, use a clay body with less contraction.
There's also a problem that looks like shivering when small sharp shards of glaze flake of the edges of work. This seem to be caused by poor adhesion of an underglaze or slip to the edges of the work and when the glaze shrinks in cooling, it pulls the loosely bonded underglaze away. The underglaze is usually poorly bonded because it has been applied to thickly or retouched to a damaged edge, applied to bone dry or bisque rather than firm leatherhard work). Bisque fire higher or soaking at top temperature can help, but the key is using the underglaze thinly.
Glaze Slop Problems
Try to keep 10-15% ball clay in the glaze. If this is not possible to have this much alumina, try 3% Australian bentonite or 1% Bentone (US white bentonite). This won’t easily mix into the glaze slop, so either thoroughly mix all the dry materials together before adding to water, or sprinkle the bentonite on the water at the top of the bucket and leave to slake for a day or two.
Materials like frits make a fragile powdery surface, difficult to handle, and difficult to paint over. Materials like clay, wollastonite, talc and zircon help make a hard surface. Adding 1.5% CMC gum will toughen a glaze surface, or adding PVA glue.
Glazes that settle can be helped by adding a few drops of ‘glaze suspender” (calcium salts) to make the clay particles repel each other. Soluble materials like bicarb soda or soda ash, salt, raw wood ash will tend settle hard in the bucket because their alkalis will flocculate the glaze slop. They will also irritate unprotected skin. But they can make beautiful glazes.
Crawling: can be caused by high shrinkage of the raw glaze surface. Glazes containing a large amount of clay or other materials with high shrinkage, like magnesium carbonate, dolomite and talc are prone to crawling. Bisque contaminated by grease or dust and a rough turned surface will also cause crawling. A thick application, or applying glazes in layers can cause more crawling. Although, like all glaze faults, crawling can be used for decorative effect, it can be cured by keeping bisque clean, glaze application thin, and changing materials to reduce shrinkage. If you can’t reduce the amount of clay or crawl prone fluxes, try weighing out half the raw clay and calcining. This is firing the raw clay to at least 600oC before mixing the glaze batch. This preshrinks the glaze before it is applied to the pots.
PinholingMost glazes go through a boiling stage, before the bubbles burst, and the glaze smooths out. If the firing is fast, the glaze may not smooth out completely, leaving pinholes. So try extending the firing, but it is usually only a problem with small kilns.
Some fluxes out gas more than others, substitute others will a lower LOI (loss on ignition). Eg wollastonite instead of whiting. Frit 4110 instead of bicarb soda.
Coarser clay bodies are more prone to pinholing than smooth clays. Change clays or soak the bisque or increase bisque temperature to 1060oC to expel as much gas as possible.
Some fluxes will turn to gas when their normal firing temperature is exceeded eg lead above about 1150oC
A lot of problems that you might call “glaze faults” are often caused by sloppy technique in forming or glaze application, like rough surface on the clay surface or edges, greasy or dusty bisque, not stirring the glaze slop thoroughly, glaze application to thick or too thin, uneven application with runs or drips, fingerprints in the wet glaze that need to be touched up, or allowing the surface to dry before over dipping etc etc. Some beautiful glazes contain ingredients that make them difficult to use.
Developing a good glazing techniques is an important skill. With experience you’ll plan how to glaze your work before you make it.
Line Blends
Line blends are a quick way of systematically testing a mix of 2 glazes or materials
Volumetric Line blend.
To make a volumetric line blend with 10 %increments.
Makes 20mls of each glaze blend, which is just enough to glaze a 75mm test tile.
Start with 2 clear plastic cups or jugs of the same size and shape.
- Weigh out 200gms of dry material for A. Mix with enough water to achieve pouring consistency. (start with 150 mls of water and then thin down more if required. The amount of water will vary for each different material.
- Weigh out 200 gms of dry material for B and equalise the volume of sample A.
- Place 11 numbered cups in a row.
- After stirring wet material A, use a syringe, to measure out 20mls into cup1, stir then 18 mls into cup2 and so forth. When all 11 cups are done, clean the syringe by sucking up clean water and expelling. Don’t take the plunger out of the syringe or it will may break.
- Now stir wet material B and measure the correct amount into each cup.
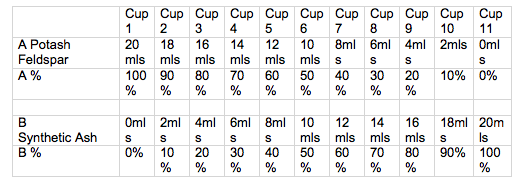
- Stir cup 1 and pour the glaze over the face of tile 1, then pour again over 2/3 of the tile, and pour again over 1/3 of the tile, so you have 3 different thicknesses. Wipe any glaze of the back and sides of the tile and label the back of the tile with underglaze or oxide before you go onto the next tile. The label should be:
- 1
A or an abbreviation of the material 100%
B 0%
Continue to glaze and label all 11tiles.
Modified line blend
A quick, but slightly less accurate method of blending colourants or a single material into a glaze.
Eg, to add iron oxide to a celadon base glaze.
Mix 100gms of the base glaze and sieve.
Weigh out 1% red iron oxide, add to base glaze and stir very thoroughly. Pour onto a tile, in 2 thicknesses, collecting all the run off and return to the glaze batch cup. Label the tile.
Weigh out another gram of oxide, stir into the glaze and pour tile 2. Label, and so forth.
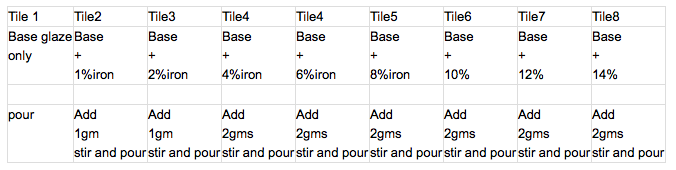